As part of a £1.8m InnovateUK research project, Plus X Innovation has partnered with circular manufacturing specialists Batch.Works and AI research spinout Matta to host and pilot an automated 3D printing facility using robotic control and AI to scale for local batch production.
During the pilot, we’re exploring how designers can use the latest advances in digital manufacturing to produce locally, with a circular flow of materials, and take advantage of the possibilities for agile product development, extreme customisation, and low-wastage production.
This research project will help us develop 3D printing into a scalable manufacturing process that could transform how we design products, making them more efficient and less wasteful and enabling designers to start to displace high-energy offshore mass-manufacture with on-demand, local manufacturing.
Learning About Cutting Edge Technologies
The very nature of this pilot means that the technology is at the cutting edge of innovation. These 3D printers are very different to the traditional models. The entire process is automated from start to end; they automatically control loading 3D printer filament material into the printers and have robotic controls to remove finished parts.
Typically, in 3D printing, there are a lot of errors. Because these new machines incorporate AI technology developed by Matta, the chance for error is greatly diminished. Using cameras mounted to the printers, the AI system can monitor the print and determine if an error is about to occur. It can either stop it before it can happen or alter and improve the process to avoid the issue.
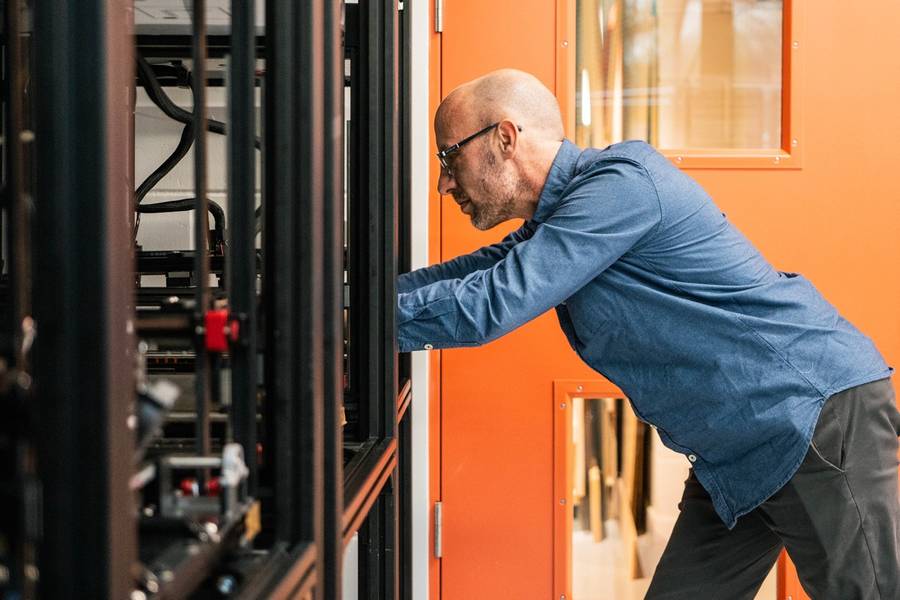
Embracing the Circular Economy
3D printing can be a less wasteful process compared to others, such as milling processes. With 3D printing, you start from nothing and add filament to create your product instead of starting with a big block and removing material until you have your part. The filament does have the potential to be more sustainable, being derived from biological sources such as corn starch rather than petrochemical plastics and can, if the product lifecycle is managed well, be ground down to be recycled into new filaments.
Also, this technology enables you to make exactly what you need, meaning you can respond to customer demand or try something out in the markets without leaving tonnes of wasted materials if it’s unsuccessful.
Finally, 3D printers can be easily installed in many locations, meaning you don’t need a big factory to produce them, can harness materials available within your location, and can distribute production much closer to customers. That means less travel for source materials, less travel for parts, and both design and manufacture being closer to the market.
Test your Designs
During the pilot, we’re hosting a series of events and one-to-one workshops for our members to learn how to use the printers and to discover from designers and engineers how to adapt their designs to be manufacturable with this technology.
We’ll be providing all the materials and offering design support. If you’re looking for support with adapting CAD files or optimising designs for 3D printing, the Plus X Innovation workshop team and Batch.Works experts will be on hand.
The manufacturing facility is available to all Plus X Innovation members who want to learn how to use these new machines. It’s an ideal scheme for any Plus X Innovation community members who wish to make a prototype or small runs of test products to send out to beta testers.
If you've got a group of early adopters, testers, and people interested in your products, and you want to submit a new design you want to test before selling to them, that would be perfect for this project.
If you’re interested in learning more about the Sustainable Smart Factory Pilot Scheme, book a tour of our workshop to learn more. Or, if you’d like to join the Brighton Plus X Innovation community, book a tour of our Brighton innovation hub.